INTERVIEW WITH KNORR-BREMSE
.
In 2018 at TRANSLOG Connect Knorr-Bremse won the 6th CEE Logistics and Supply Chain Excellence Award in the manufacturer category!
.
Knorr-Bremse Group - based in Munich - is the world’s leading manufacturer of braking systems and supplier of additional sub-systems for rail and commercial vehicles. For more than 110 years now the company has pioneered the development, production, marketing and servicing of state-of-the-art braking systems. In 2017, Knorr-Bremse reported sales of EUR 6.24 billion and employed some 28,000 people worldwide.
Knorr-Bremse Systems for Commercial Vehicles provides a range of services on representative technologies such as pneumatics, mechanics, electronics and complex control engineering. The individual growth of any of its current five European manufacturing locations depends partly on external factors such as the European truck production rate or the position of its product portfolio on the product lifecycle and the market demand to resupply those parts, or on internal factors such as the share of production won from the wide variety of product families that are offered by the production technologies that Knorr-Bremse possesses.
To learn more about their award winning project we asked Gábor Salamon, Supply Chain Director of Knorr-Bremse Systems about the project which made them win the award!
Mr Gábor Salamon works for Knorr-Bremse Truck Hungary since the year 2009 as Logistics Manager and since 2017 as Supply Chain Director. His current responsibilities include supplier integration, procurement of production components and sales merchandise, production planning, lean management and warehousing, customer order management and outbound logistics. He also bear the title of the Export Control Officer of the company.
.
Which challenges have you addressed in the project which won the award?
Gábor Salamon "Knorr-Bremse has executed a high number of production relocation projects since the year 2014 in which the Hungarian plant in Kecskemét was awarded as many as 43 (mainly high runner) production lines relocated from three other Knorr-Bremse factories. In order to enable the hosting of these product families the Kecskemét plant took the opportunity to build a new and state-of-the-art production facility which became fully operational in the year 2014. Since then competitiveness was continuously on the rise, since product families turning close to the end of their product lifecycle, or were classified as low runners were either relocated out from Kecskemét or simply streamlined, whereas product families and new technologies were awarded and moved in to Kecskemét. The product range of the Kecskemét plant was changed by 68% within this roughly four-year period of moving the production of product families. In the automotive industry, such a change is controlled by very strict rules driven by customer approvals. To comply with them, a precise and elaborate methodology has been developed in order that customers may perceive only the positive effects of the relocation project.
The biggest challenge is to assure that customers do not recognise any disadvantage from the relocation through ensuring, that continuity of supply during the course of the relocation is fully provided. Above that, each project element represents a special challenge in the course of relocation. Project elements include the design and buildup of buffer stock covering customer orders from disassembly of the lines until the first deliveries to customers from the new location, the training of the step-by-step production process, selecting and organising the safe delivery of the production equipment and their setting up at the receiving location, transfer of component kits for test production, picking and dispatch of production components and spare parts, the handing over of all documents, drawings, packaging instructions, maintenance manuals that are essential to the standard operation of the lines, the process of how and when suppliers and customers are involved and how first the supplier purchase orders, then as part number by part number the buffer stock is being consumed, the customer orders are being taken over by the receiving location, the change of the external supply chain in line with the change of the number and location of suppliers and customers, the altering of the internal supply chain for production supply, and many more aspects."
What were the major achievements after the project had been implemented?
Gábor Salamon "As complex as it is unique, this project type is really exciting for logistics professionals. The major achievement of such a project is the smooth transition of processes that are beneficial for both the suppliers, the production location and the customers."
In your opinion how is the award supporting the developments of logistics in the CEE region?
Gábor Salamon "In the automotive industry such a change is controlled by very strict rules driven by customer approvals. To comply with them, a precise and elaborate methodology has been developed in order that customers may perceive only the positive effects of the relocation project. The increase of production capabilities and output in the CEE region is a direct benefit derived when a relocation project is completed."
Which are the biggest challenges your department is currently facing?
What type of new solutions or methods are you planning to introduce in your current and upcoming project?
Gábor Salamon "I think the biggest challenge is to follow-up growth. Tools to comply with such a challenge is to improve the business processes, not withstanding the need for new technologies. Taking advantage of these new tools are enticing, but adoption and onboarding might be overwhelming. Customer service improvement is another challenge. Customers want full transperency on many aspects of the supply chain, and they want low price. Keeping prices low where fuel prices and overhead costs are increasing due to manpower shortage is not easy. Processing an enormous amount of information is another challenge that logistics managers need to face. Logistics managers have to deal with a lot of figures and data on a daily basis, besides coordinating smooth discharge of operations. Thanks to globalisation, logistics management is turning into a multi-layered job where managers are expected to keep tabs on multiple supply chains simultaneously. You don’t just need to deliver goods on time but also offer customised services to different suppliers and customers in terms of packages and pricing. The keyword for success in this scenario is flexibility. Using a software system that can automate the process of projecting different services to different customers can not only save time and effort on the managerial level but also bring added accuracy to data compilation and compliance to different compliance to regulations."
.
.
If you think your solution is cutting-edge and should be recognized by the industry, apply for the 7th CEE Logistics & Supply Chain Management Excellence Award and put your business in the spotlight by presenting your solution at the upcoming TRANSLOG Connect Congress!
.
Follow us and join our online professional business community on social media!
Did you like the article?
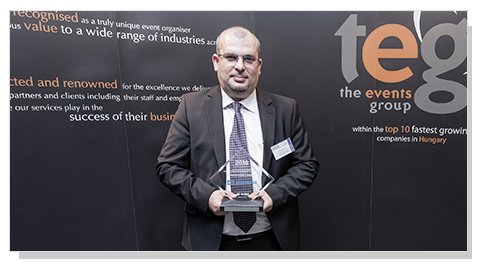